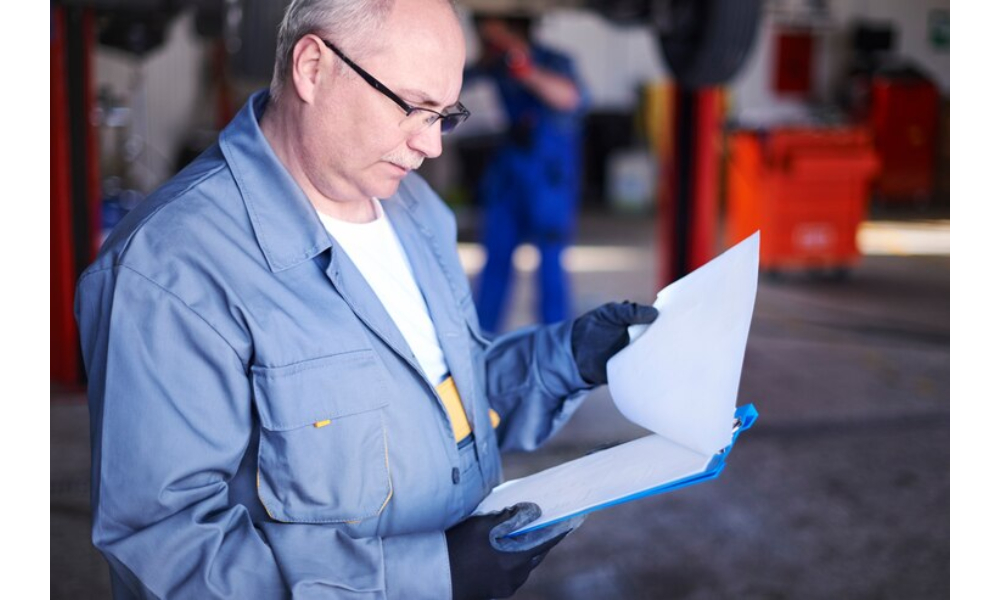
Upgrading industrial operations is essential for maintaining competitiveness and increasing productivity. As businesses evolve, adopting modern technologies and systems can significantly improve efficiency, reduce costs, and enhance safety. When planning an upgrade, it’s crucial to consider several key factors to ensure a seamless transition and long-term success.
1. Importance of Business Electrical Upgrades
An often overlooked yet critical aspect of upgrading industrial operations is ensuring that your business electrical infrastructure can handle the demands of new technology. As businesses expand and incorporate energy-intensive machinery, having a robust and modern electrical system is vital. Outdated wiring, inadequate power distribution, and insufficient voltage levels can lead to costly downtime or even equipment damage.
Upgrading your electrical system is not just about capacity—it’s also about safety and compliance. Newer electrical systems are often more energy-efficient, reducing overall consumption and lowering operational costs. Furthermore, they are designed to meet the latest safety standards, minimizing the risk of electrical hazards. Engaging an experienced business electrical service provider will ensure that your system meets current industry standards, allowing your business to run smoothly and safely.
2. Streamlining Operations with Industrial Automation System Installation
Another critical consideration is the implementation of an industrial automation system. These systems are designed to control and monitor industrial processes, allowing businesses to optimize performance and reduce human error. Automation enhances consistency, improves quality control, and can lead to significant cost savings over time. From assembly lines to material handling, automation can be applied across various operations.
When planning an industrial automation system installation, it’s essential to choose a system that aligns with your business needs. A thorough assessment of your current operations will help identify areas where automation can deliver the most value. This may involve integrating sensors, programmable logic controllers (PLCs), and robots into existing processes. By automating repetitive tasks, you free up human resources for more strategic roles, thereby increasing productivity and operational efficiency.
3. Training and Skill Development for Employees
While upgrading systems and infrastructure is crucial, the human factor cannot be ignored. Investing in training and skill development for employees is just as important as upgrading technology. New machinery and systems often come with a learning curve, and ensuring that your workforce is adequately trained is key to maximizing the potential of these upgrades.
Training should focus not only on technical skills but also on fostering a culture of adaptability and continuous improvement. With the right training programs in place, employees will be able to navigate the new systems confidently, making the transition smoother and reducing the risk of costly mistakes. Providing ongoing education also helps retain top talent and encourages a proactive approach to operational challenges.
4. Maintaining Flexibility and Scalability for Future Growth
As industries evolve, businesses need to plan upgrades with the future in mind. Flexibility and scalability are essential considerations when upgrading industrial operations. Ensure that new systems and processes are adaptable to accommodate future changes or expansions. Whether it’s adding new machinery, expanding your production line, or incorporating emerging technologies, having scalable solutions in place can help you avoid costly overhauls down the road.
When upgrading your industrial operations, consider how easily new components can be integrated into existing systems. Choose technologies that can evolve with your business needs and provide long-term value. By planning with growth in mind, you position your business for success in the years to come.
Conclusion
Upgrading industrial operations involves careful planning and strategic investments in various aspects, including business electrical systems and industrial automation. By focusing on these key considerations—upgrading electrical infrastructure, implementing automation systems, training employees, and planning for scalability—businesses can optimize operations, enhance efficiency, and remain competitive in a rapidly evolving marketplace.